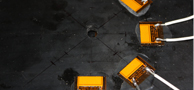
Cutting/Drilling, Assembly, Operation Monitoring and Its Modeling
Strain monitoring is conducted through cutting/ drilling, assembly, and operation process using multiplexed FBG or distributed optical fiber sensor systems. Strain history can be an efficient way to prove the validity of various manufacturing processes. Theoretical and numerical modeling is also developed.
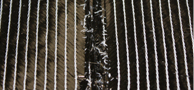
Fabrication Process Monitoring and Its Modeling
Thermal residual strain and temperature distribution of large-scale composite structures is monitored using optical fiber sensor systems. Theoretical and numerical modeling is developed based on the measured results for both autoclave processing and VaRTM (Vacuum-assisted Resin Transfer Molding) processing.
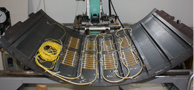
Experimental Micromechanics of Composites - In-situ Microscopic Damage Observation and Modeling
New types of composites are tested including carbon nanotube (CNT) polymer composites, ceramic fiber/matrix composites, and high-temperature polyimide matrix composites. Theoretical and numerical modeling is established based on the observed failure process in order to provide necessary feedback data for material design.
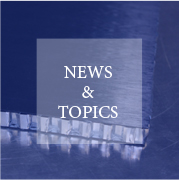
-
Professor Nobuo Takeda Elected as President of ICCM (International Committee of Composite Materials)
ICCM20, primary symposium on composite materials, was held in Copenhagen, Denmark, on July 20 - 24, 2015, Executive Committee and General Assembly of ICCM selected Prof. Takeda as President, first from Asia Region.
Professor Nobuo Takeda Awarded "NDE Lifetime Achievement Award"
Prof. Takeda was awarded SPIE Smart Structures/NDE 2014 in SPIE* 2014 San Diego on March 11, 2014.
* The international society for optics and photonics