Current Research
1. Experimental Micromechanics of Composites
- Microscopic In-situ Observation and Modeling of Damage Initiation and Growth Process
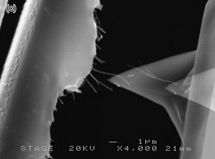
measurement of CNT/epoxy composites
Microscopic in-situ observation of damage initiation and growth process is conducted using SEM/TEM with loading apparatus. Several new types of composites are tested including carbon nanotube (CNT) polymer composites, ceramic fiber/matrix composites, and high-temperature polyimide matrix composites. Theoretical and numerical modeling is also established based on the observed failure process in order to provide necessary feedback data for material design. Such efforts are necessary to develop efficient composites for damage tolerance design.
- Deformation and interfacial strength measurement of CNT/epoxy composites and modeling (Fig. 1) (JAXA, Advanced Composite Research Center)
- Damage tolerance evaluation of SiC/SiC composites (IHI, METI Project)
2. Fabrication Process Monitoring and Its Modeling
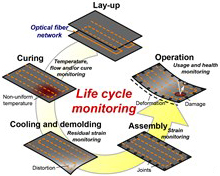
Structures
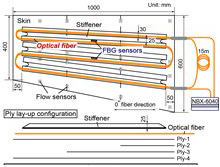
Non-uniform material quality is often of serious concern in large composite structures. Thermal residual strain and temperature distribution of large-scale composite structures is monitored using a distributed optical fiber sensor system and a multiplexed FBG (Fiber Bragg Grating) sensor system. Theoretical and numerical modeling is developed based on the measured results for both autoclave processing and VaRTM (Vacuum-assisted Resin Transfer Molding) processing. Fabrication process monitoring is part of life cycle monitoring (LCM) throughout the life of the CFRP structure.
- Life cycle monitoring of CFRP Structures (Fig. 2) (MEXT Grant-in-Aid for Scientific Research)
- Thermal residual strain measurement of curved CFRP structures and shape/process optimization (MEXT Grant-in-Aid for Scientific Research, Mitsubishi Heavy Industries)
- Temperature and strain distribution monitoring of large-scale VaRTM structures (Fig. 3, Fig.4) (CRC-ACS, Australia)
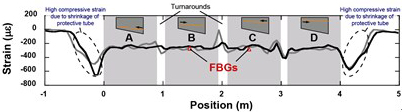
3. Cutting/Drilling, Assembly, Operation Monitoring and Its Modeling
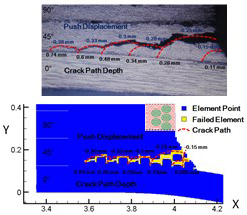
Toughened CFRP Laminates
Strain monitoring is conducted through cutting/ drilling, assembly, and operation process using multiplexed FBG or distributed optical fiber sensor systems. Strain history can be an efficient way to prove the validity of various manufacturing processes. Theoretical and numerical modeling is also developed.
- Cutting/drilling simulation of CFRP laminates (Fig. 5) (MEXT Grant-in-Aid for Scientific Research)
- Damage growth monitoring of CFRP bolted joints using distributed optical fiber sensors (Fig. 6), (Collaboration with Kyoto Univ.)
- Optical Fiber Based Structural Health Monitoring Technologies for Aircraft Composite Structures (Sokeizai Center/METI Project, KHI, FHI, MHI, MELCO)
- JASTAC (The Japan Airbus SHM Technology for Aircraft Composite) Project (Sokeizai Center, Airbus)
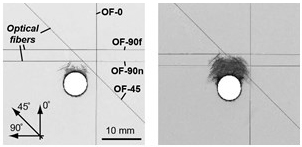
Fig. 6 Numerical Simulation of Residual Strain in
Damaged Bolted CFRP Laminates and Damage Detection
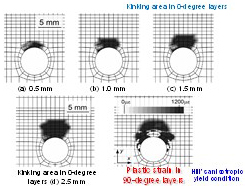
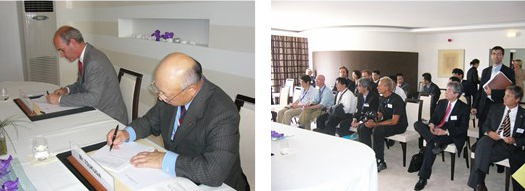